Книга: Интернет: Заметки научного сотрудника
57. Композиционные материалы
57. Композиционные материалы
– А что потом? – спрашивали меня те немногие, кто прочитали первый вариант рассказа про интервью. – И что такое эти самые композиционные материалы? И вообще, как это – public компания и как это она «поднимает» 60 миллионов долларов? Ну ладно, продолжим, и остановимся на, так сказать, технических моментах, которые я проскочил в первой части повествования. Будем считать, что это иллюстрация американского капитализма в действии, точнее, его финансово-организационной стороны с последующим техническим результатом.
Описанный выше мой переход из Гарвардского университета произошел в только что образованную компанию, которая получила название «Термо Файберджен» (Th ermo Fibergen). Это было в 1996 году. Название компании складывалось из двух понятий. «Термо» – это от имени нашей материнской компании «Термо Электрон» (Th ermo Electron), а «Файбер» – это по-английски «волокно», в данном случае целлюлозное волокно. У компании «Термо Электрон» было 27 дочерних компаний, и наша была одна из самых последних. Причем из этих 27 компаний 23 были «паблик компании», то есть те, которые инвестируются за счет широкой общественности, и каждый инвестор или «мини-инвестор», вкладывая деньги в компанию, становится ее совладельцем – в той мере, в которой вложил в нее деньги. Степень «совладения» определяется количеством акций, которые «совладелец» приобрел. Чем дешевле акции, тем больше их можно приобрести за те же вложенные деньги, тем больше степень «совладения» компанией инвестором. Плюс для «паблик» компании в том, что она получает крупные денежные вливания от общественности, и на эти деньги компания платит зарплату сотрудникам, приобретает приборы и оборудование, арендует или приобретает здания и помещения, и производит – в случае удачи – продукцию, продавая которую, компания растет и развивается. Минус для «паблик» компании в том, что она должна в деталях отчитываться перед общественностью за свою деятельность. «Паблик» компания должна быть «прозрачной» перед общественностью.
Стиль работы компании «Термо Электрон», образованной еще в 1950-х годах выпускником MIT (Массачусетского технологического института) и его братом, был в том, что как только руководство компании ощущало новое направление в технологии, оно образовывало очередную новую дочернюю компанию и скоро делало ее «паблик». Тем самым «Термо Электрон», оказавшись в итоге многомиллиардной компанией, оставалась компанией по размерам довольно маленькой. Она, как щупальца спрута, простирала свои дочерние компании, покрывая области от производства шагающих экскаваторов до аппаратов искусственного сердца, от самого современного научного оборудования до космической технологии, от кардиологии до утилизации промышленных отходов. Эта весьма необычная «финансовая модель» компании «Термо Электрон» многократно описывалась в ведущих финансовых журналах мира. А само небольшое элегантное здание компании, выстроенное среди скал на красивейшем месте в ближнем пригороде Бостона, с видом на лесные озера, вмещало только штаб-квартиру компании, патентные отделы, изысканный ресторан для сотрудников и несколько офисов и конференц-залов.
Наша компания «Термо Файберджен» являлась фактически внучкой «Термо Электрона», так как сначала отпочковался «Термо Файбертек», который занялся производством оборудования для бумажных фабрик, а от «Файбертека» уже отпочковался «Файберджен». Как я уже упоминал выше, «Файберджен» был создан для того, чтобы найти коммерческую область применения огромным количествам отходов производства бумаги в виде коротковолокнистой бумажной пульпы, перемешанной с минералами, главным образом карбонатом кальция (мел) и алюмосиликатами (каолин, или особая белая глина). Эти отходы имеют вид влажной массы, типа глины, и наполовину состоят из целлюлозы и наполовину из минералов.
Еще я писал, что эти материалы практически никому не были нужны, поскольку тем, кого интересует целлюлоза, не нужны перемешанные с ней минералы, а тех, кому нужны минералы, не интересует целлюлоза. Вот для того, чтобы найти, что из этого материала можно делать такое, чтобы продавать за немалые деньги, и была создана наша компания. Напоминаю, что коммерческие компании создают с единственной целью – делать деньги. Все остальное – лишь привходящие факторы, в конечном итоге подчиненные главной задаче. На меня были возложены обязанности руководителя исследований и разработок компании – сначала как менеджера по исследованиям и разработкам, а затем как вице-президента компании.
Проработав несколько вариантов и получив несколько патентов США на новые разработанные нами процессы использования этих материалов, мы остановились на получении микрогранул. Процесс выглядел так: смесь волокон и минералов диспергировалась в воздухе, и образовавшиеся мелкие частицы в специальном аппарате с большой скоростью выстреливались друг в друга, образуя слипшиеся частицы, или агломераты. Размер агломератов зависел от двух главных факторов – количества воды (влажности) в исходном материале и скорости выстреливания. Потом микрогранулы сушились в вибрационной печи и фракционировались по размерам, от миллиметра до десятых долей миллиметра в диаметре. Эти гранулы мы использовали как наполнители пластмасс при экструзии композиционных материалов.
Экструзия – это процесс выдавливания вязких материалов через фильеры с последующим затвердеванием материалов с образованием изделий нужной формы. Фарширование мяса на мясорубке – это экструзия мяса с образованием фарша. Ну, почти экструзия, хотя там продукт не совсем затвердевает. Экструзия алюминия – широко известный процесс в металлургии. У нас была экструзия наполненных полимеров. Аппарат для экструзии похож на большую мясорубку, только производит сотни килограммов готовой продукции в час. В загрузочную камеру этой «мясорубки» засыпают гранулы полиэтилена, измельченное целлюлозное волокно и наши микрогранулы, которые производятся на нашем же соседнем – через улицу – заводе в количестве сорока тысяч тонн в год. А также много важных дополнительных ингредиентов – красителей, детергентов, антиоксидантов и прочих стабилизаторов.
Вся эта масса винтом, как в мясорубке, продавливается в соседнюю зону, которая находится под сильным нагреванием. Плюс немало тепла производится от перемешивания и трения частиц между собой. В этой зоне пластмасса плавится и перемешивается с остальными составляющими смеси, и продвигается тем же винтом дальше по цилиндру, опять же как в мясорубке. Только диаметр этого цилиндра гораздо больше. Вязкий расплав проходит по всей длине цилиндра, метров пять, и в итоге продавливается через отверстие нужной формы, охлаждается, подсасывается вакуумом для придания более правильной формы конечному изделию, проходит через водяную ванну для дополнительного охлаждения, обрабатывается с двух сторон стальными щетками и приобретает окончательную форму пустотелой строительной доски стандартного размера пять с половиной дюймов шириной и дюйм с четвертью толщиной, или, как обозначают по нормам строительных материалов, 5/4 ? 6. Эта непрерывно выходящая с конвейера доска пилится по длине на 20-, 16– и 12-футовые, упаковывается в штабеля и идет на предпродажный склад здесь же, на нашем заводе.
Легко это описать, но сам процесс имеет массу тонкостей. Если расплав чуть недогрет, он твердеет и продирается через фильеру с образованием раковин и прочих дефектов. Если он чуть перегрет, он выливается через фильеру, будучи еще относительно жидким, и не приобретает нужной формы. Если охлаждение быстрее необходимого, полимер «замерзает» в напряженном виде, и эти напряжения потом себя проявят в виде искореженной доски или доски с заметной усадкой. Если скорость движения расплава выше необходимой, температура его поднимется из-за внутреннего трения, со всеми вытекающими последствиями перегретого материала. Этот перечень можно продолжать.
И теперь самое главное – зачем мы это делаем и кому эта доска нужна. То, что мы делаем, называется строительные целлюлозо-полимерные композиционные материалы. Это – замена древесины, в данном случае деревянных досок. В первую очередь – для покрытия так называемых «деков», очень популярных в США. Полного аналога американских деков в России, да и во всей Европе нет, хотя мода постепенно поворачивается к декам и по европейскую сторону океана. Дек – это веранда, часто довольно широкая и длинная, обычно окаймленная перилами, которая примыкает к дому на уровне первого или второго этажа. Это, фактически, продолжение или расширение дома. На деке отдыхают, покачиваясь в креслах-качалках, приветственно помахивая руками проходящим или проезжающим соседям. На деке играют дети. На деках жарят мясо для собравшейся компании, на деках собираются и болтают гости, потягивая вино и пиво. И вот для этих самых деков и предназначены в первую очередь наши композиционные доски.
Дерево – прекрасный материал, но со многими недостатками, особенно для «наружного» применения, в частности на деках. Дерево довольно быстро гниет, его разрушают микроорганизмы, термиты и прочие древоточцы. Оно впитывает много воды – при погружении обычной строительной древесины в воду она впитывает влагу в количестве 24 % от своего веса за первые сутки. Это в свою очередь вызывает довольно сильное набухание древесины, и не только. Влага в древесине опять же приводит к довольно быстрому ее гниению. Чтобы это замедлить, дерево красят. Через некоторое время краска слезает, опять же в первую очередь от воды, и приходится все это дело перекрашивать. Если не красить, древесина быстро темнеет за счет окисления кислородом воздуха. Окисление приводит к уменьшению прочности и опять же к разрушению. Это – не говоря о занозах от грубо обработанной древесины.
Для того чтобы замедлить гниение и разрушение термитами, строительную древесину пропитывают солями мышьяка. В США такую древесину называют «древесина, обработанная давлением». Про мышьяк в названии деликатно умалчивают. Но борцы за сохранность окружающей среды и здоровья человека добрались и до такой древесины. Под всё усиливающимся нажимом активистов уже практически произошло полное запрещение производства и применения древесины, содержащей соли мышьяка. И в США, и теперь в Европе. И общественное мнение активно настраивается против такой древесины. Я это впервые ощутил еще пару лет назад, когда заехал в пригороде Бостона в «ламбер-ярд», или специализированный магазин по продаже строительных материалов из дерева. Попросил напилить мне несколько полутораметровых досок, тех самых, «обработанных давлением». И получил отказ. Мне было сказано, что недавно поступил запрет на распил рабочими магазина этих самых досок. По причине охраны здоровья рабочих. На вопрос – а что мне делать, поскольку шестиметровые доски ко мне в машину не войдут, мне было исключительно любезно отвечено, что магазин будет счастлив доставить мне эти доски на грузовике, и я могу сам пилить их на свое здоровье.
Пришлось так и сделать. В этом смысле наши композиционные доски – просто подарок потребителю, причем подарок своевременный. Они совершенно не содержат каких-либо вредных веществ, они не могут занозить, и по ним можно ходить босиком, совершенно не беспокоясь о типичных последствиях ходьбы по доскам деревянным. Кстати, они сделаны изящно-шершавыми благодаря специальной обработке металлическими щетками. Они совершенно однородные по материалу, они не выгорают под действием солнца, так как содержат неорганические красители (окислы железа), которые выгореть или вообще окислиться дальше не могут, поскольку окислились уже до мыслимого предела. Они не повреждаются микробами, их не трогают древоточцы, их не нужно красить и перекрашивать, поскольку мы их выпускаем уже окрашенными практически навечно. Наконец, один из вариантов наших композиционных досок имеет форму ребра «ласточкин хвост», как паркет, и при установке на деке ребро одной доски прибивают или привинчивают и покрывают его пазом соседней доски. Таким образом на всем деке не видно ни одного гвоздя. Только сплошное «деревянное» покрытие.
Композиционные доски пилятся, режутся, прибиваются гвоздями или привинчиваются шурупами совершенно так же, как и обычные деревянные доски. Наши композиционные доски впитывают воду в 10–20 раз меньше, чем обычные деревянные доски.
И еще одна немаловажная особенность. Те, кто покупал деревянные доски в магазине, по крайней мере в США, знают, сколько досок надо перебросать, чтобы найти одну приличной формы. Складывается устойчивое ощущение, что хороших досок нынче просто нет. Сплошь покореженные, с вызывающе торчащими сучками, с расщепленными краями, вычурно выгнутые… Наши композиционные – идеальной формы и конфигурации, комфортабельно шероховатые, никаких сучков и задоринок.
Наши доски поступают на рынок под названием GeoDeck. Из них в США построено уже 50 тысяч деков. Более того, в то время, когда я это пишу, наше производство отстает от спроса на две-три недели. Иначе говоря, покупают быстрее, чем мы их производим. Только что мы получили информацию из Consumer Report – журнала, следящего за качеством товаров в США и информирующего об этом потребителя. Так вот, только что наш GeoDeck получил статус Best Buy. Это – успех.
С точки зрения научного сотрудника, это – исключительно захватывающая область исследований и разработок. В ней сходятся полимерная химия, физика полимеров, химическая инженерия, сопромат, а также то, что называется «наука материалов», или материаловедение. Здесь же – физическая химия целлюлозы, реология расплавов, и в особенности реология неньютоновских жидкостей. Это только начало перечня. Универсальных специалистов по всем этим областям нет. К тому же успех определяется взаимодействием и правильной координацией научных исследований с заводским, промышленным производством.
Это все непросто. Но, как известно, трус не играет в хоккей. Только что я вернулся из Торонто, Канада, с крупнейшего конгресса по строительным композиционным материалам, где делал доклад на тему «Композиционные материалы в настоящем, реальном мире». Смысл названия был в том, что почти все публикуемые исследования композиционных материалов, за редким исключением, проводятся в университетах и прочих «академических» лабораториях. К ним полностью применимо высказывание – «страшно далеки они от народа». Настоящих композиционных деков они, как правило, в глаза не видели. Разрабатываются материалы, которые просто не смогут найти применение в коммерческих деках по простой причине – экономической. Изучаются не настоящие крупногабаритные «доски», а узенькие полоски материалов, получаемых на маленьких лабораторных установках, в совершенно искусственных зонах температур и давлений, в отличие от промышленных установок. Нет сомнения, что эти «академические» исследования обогащают науку о композиционных материалах, но это, за очень редким исключением, не имеет никакого отношения к поведению деков «в поле». К тому, как идет их старение, выгорание и разрушение в настоящих природных условиях, как ежедневные температурные перепады «раскачивают» композиционные доски и к чему это приводит в отношении изменения их свойств, как «плывут» наполненные полимеры при жаре, скажем, Техаса и Аризоны, при влажности и микрофлоре Флориды. Как они, находясь под снегом где-нибудь в Миннесоте или Висконсине, реагируют на многократные оттепели, на многократные замерзания-оттаивания. Таких исследований и их соответствующих адекватных моделирований в лабораторных условиях практически не было. Не было до доклада в Торонто. Неудивительно, что слушатели стояли в проходах. И это не пустое бахвальство, а законная гордость научного сотрудника за свою работу.
Чтобы скомпенсировать возможное впечатление читателя от «головокружения от успехов», поделюсь обратной стороной медали – головокружительным срывом, который потерпела наша компания в самый разгар триумфального шествия композиционных досок. Это был срыв, от которого иные компании разоряются, терпят банкротство. И это тоже иллюстрация того, что может довольно внезапно произойти с любой успешной компанией. Часть этого греха лежит и на мне – недосмотрел. Хотя в вину мне этот технологический срыв не поставили.
А произошло вот что. Впрочем, сначала предыстория. Полимеры на солнце окисляются. И под действием ультрафиолетового света, и тем более под действием достаточно высокой температуры поверхности полимера при солнечном нагреве. А само окисление происходит под действием кислорода воздуха. В полной мере это относится к нашим композиционным доскам. Более того, в отличие от чистых полимеров композиционные доски, о которых идет речь, содержат в своем составе целую обойму катализаторов окисления – металлов, которые входят в состав красителей, наполнителей, лубрикантов и прочих ингредиентов. Влага – тоже катализатор окисления. Короче, если в состав смеси не вводить специальные антиоксиданты, то композиционные материалы начнут вскоре активно окисляться и крошиться. А если вводить нужные количества антиоксидантов, то срок службы композиционных досок может легко превышать двадцать лет. Именно на этот срок дается гарантия производителя.
Ну и теперь драматическая история. Наш завод забыл добавить в композиционную смесь антиоксиданты и не добавлял их целый год (!). Поскольку на этой стадии процесс уже давно вышел из зоны ответственности отдела исследований и разработок, то мы и не знали. Технолог завода рапортует, что все в порядке, заводской отдел контроля качества продукции содержание антиоксидантов не измеряет (точнее, тогда не измерял), да и как их измерять-то? Их содержание – десятые доли процента, это никто в нашей отрасли промышленности не мониторит, просто добавляют, и всё. По виду доска замечательная, все механические параметры в норме, идет с колес в продажу, как положено, как уже привыкли.
А она на самом деле начинает крошиться под горячим солнцем Флориды или там Техаса или Аризоны уже через год-другой. Но тогда мы этого знать еще не могли.
И вот поехал я на завод в штат Висконсин по какому-то рутинному делу. И заодно решил зачерпнуть у них там порошок антиоксиданта для своей лаборатории в пригороде Бостона, у нас как раз кончился. Пошел в цех, где готовят сухие смеси при загрузке в компаундер. Хожу – что такое, не вижу антиоксиданта. Ирганокс называется. Всё остальное есть, а ирганокса нет. И сыпят те ребята-операторы в машину неполную смесь. Что за ерунда!
Я – к технологу завода. Тот побледнел, и – к вице-президенту по производству, что, мол, беда, черт-те с какого времени нарушен технологический процесс, выпускаем без антиоксиданта. И как показала тут же документация – выпускали так целый год. В тот же день состав композиционного материала вернули на место. А вскоре и рекламации пошли, в первую очередь из южных штатов, как и следовало ожидать. Пришлось оперативно отзывать от оптовиков продукцию, выпущенную за целый год, и заменять деки, уже построенные из той продукции. На это ушло несколько миллионов долларов. Цена технологического промаха. И мне пришлось по стране полетать, объясняя научные основы заводской ошибки, точнее того, к чему она привела. В тот год я сменил более шестидесяти самолетов.
Но нет худа без добра. Мы разобрались в механизме процесса быстрого старения композиционных материалов, разработали методы количественного определения антиоксидантов в материалах, поставили эти методы на заводе как обязательные для ОТК, или QC по-нашему, и всё это, судя по всему, имеет место только в нашей компании, и ни у кого из конкурентов. Правда, это далось дорогой ценой. К счастью, судебных исков не было. Пока.
Теперь антиоксиданты добавляем с запасом, и композиционные доски стали еще лучше, чем до описанного инцидента.
Сейчас мы разрабатываем композиционную кровлю на крышу нескольких видов. То, что в США называют «слэйт», «шейк» и «Дабл Роман (Double Roman)». «Слэйт» в своей природной версии – это дорогие материалы. Они вырубаются из слоистого камня и, естественно, являются тяжелыми и хрупкими. Тяжелые – это не только трудности подъема на крышу пачек плоских каменных листов. Это еще и повышенные требования к прочности несущих конструкций. То же самое относится и к «Дабл Роман», волнистой черепице из обожженной глины, обычно столь знакомого нам красноватого цвета. «Дабл» – это относится к двойным размерам «листа» этой черепицы. «Шейк» – это исходно кедровые бруски разного размера, которые укладываются на крышу. В США все эти материалы дороги, как, впрочем, и все природные материалы. Но ход развития рынка диктует более дешевые, легкие, искусственные строительные материалы. Они, как правило, менее долговечны по сравнению с природным камнем или керамической черепицей, но это реалии сегодняшней жизни. Почти все вокруг нас ныне – синтетика, заменители. Стекло, бетон, пластмассы. Покупатель давно привык к тому, что вещи не вечны. Он, покупатель, хочет дешевые, легкие материалы, с которыми, помимо прочего, еще и легко работать. Американец в среднем меняет свое жилье семь раз за жизнь. Какая там вечность…
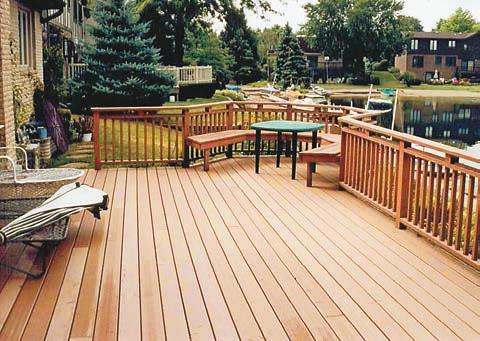
Наши полимерные композиционные материалы выглядят как настоящие черепицы. Плоские серые «слэйты», только легкие, по форме плотно пригнанные друг к другу, с отверстиями для кровельных гвоздей. Они практически не бьются, один человек без особого труда покрывает большую крышу за несколько часов. В итоге финансовый выигрыш двойной – сама крыша дешевле, и работа стоит дешевле, а это в США часто самое дорогое. Но разработать такие кровельные композиционные материалы вдвойне непросто. Крыша нагревается довольно сильно, особенно крыша темная. Ультрафиолет. Полимерные материалы окисляются и стареют. Но это нам уже знакомо. Опять же, нет худа без добра. Это я к тому, что крупная ошибка с досками помогла нам на другом фронте. Требования рынка к высококачественным кровельным материалам – не менее пятидесяти лет. К менее качественным, типа асфальтовой кровли, – лет пятнадцать. Наши композиционные должны служить не менее 30–50 лет.
Вот эту задачу мы сейчас решаем.
- 1. Короткое вступление. Немного о жизни
- 2. МГУ. Много лет назад
- 3. Наука на чердаке, или Влияние времени дня на кинетику химической реакции
- 4. Про «несломатые дома» и английский язык
- 5. Где триггер? Как из закоренелого троечника стать отличником
- 6. Четвертый этаж
- 7. Поехали
- 8. Целина, словотворчество и начало научной работы на кафедре
- 9. Дисперсия оптического вращения. Карл Джерасси и его книги
- 10. Интернет образца 1982 года. Как это начиналось в Советском Союзе
- 11. Всемирная паутина эпохи застоя. Как это было в СССР – продолжение
- 12. Попытки легализоваться в Интернете
- 13. Нобелевский симпозиум
- 14. Капустин Яр
- 15. Что такое специфичность ферментативного катализа
- 16. Рецепт для юношей (и девушек), желающих защитить докторскую диссертацию
- 17. Рождение Дня химика
- 18. Дымовая шашка
- 19. Чехословакия–1967 и после
- 20. О риске занятий научной работой по ночам. А также про крыс и хомяков
- 21. Получение диплома МГУ. Сахалин
- 22. Непричесанные мысли о науке. Конференции молодых ученых
- 23. О принципиальной разнице между инженером и ученым. И еще – о приоритете в науке
- 24. Иммобилизованные ферменты
- 25. Целина и романтика. Мои родители и Сочи
- 26. Работа ведущим всесоюзной научной телепрограммы
- 27. Как не надо смешивать лекции и выпивку
- 28. Целлюлоза и ее ферментативный гидролиз. Биотехнология целлюлозы
- 29. «Паровой взрыв» целлюлозы и канадский парламент
- 30. Энергетика в Италии. Чернобыль
- 31. Всемирная академия наук и искусств
- 32. Поездка в США, 1974 год. Преамбула
- 33. Поездка в США, 1974 год. Первые впечатления
- 34. Поездка в США, 1974 год. Английский язык
- 35. Английский язык для взрослых
- 36. Поездка в США, 1974 год. Как нас лечили от культурного шока
- 37. Нью-Йорк, 1974 год
- 38. Русская эскадра в Бостоне
- 39. Президент Израиля
- 40. Гарвард и ангиогенез раковых опухолей. История длиной в четверть века
- 41. Новое лекарство от алкоголизма
- 42. Венесуэльские алкоголики
- 43. Рубаи
- 44. Ленин и музыка
- 45. Моя милиция
- 46. Маньяна
- 47. Багира
- 48. Кино с Целиковской
- 49. Письма из Бостона. Письмо первое
- 50. Письма из Бостона. Письмо второе
- 51. Письма из Бостона. Письмо третье
- 52. Присяжные заседатели
- 53. История спиртных напитков
- 54. Паспорт
- 55. Маркет Америка
- 56. Интервью
- 57. Композиционные материалы
- 58. Как закалялась сталь. Действие первое. Начало
- 59. Как закалялась сталь. Действие второе. Берегитесь никеля. Но не в составе нержавеющей стали
- 60. Как закалялась сталь. Действие третье. Об академиках Нью-Йоркской академии наук и других титулах в США
- 61. Как закалялась сталь. Действие четвертое. «Цептер» против Сосонкина в федеральном суде
- 62. Рецензия на рецензии. О жанре Суворова-Резуна
- 63. Паспорт-2
- 64. Калории и килокалории на кухне, в спортзале и в спальне
- 65. О биохимии излишнего веса
- 66. Как построить мускулистую талию (у мужчин). Женщинам можно не читать
- 67. Ещё немного об МГУ и о коллегах
- 68. Дорога. Попытка фантазийного рассказа
- 69. Парадигма
- 70. Речь Цезаря на процессе Катилины
- 71. Се – Человек
- 72. Се – Человек. О женщинах
- 73. Умереть за княжну
- 74. Умереть за княжну. Опознать царя
- 75. Умереть за княжну. Свистопляска
- 76. Хинди – руси бхай-бхай
- 77. «Служба кровию и смертию». Дворяне и дети боярские
- 78. «Служба кровию и смертию». Испомещение служилых
- 79. «Служба кровию и смертию». Смутное время и начало дому Романовых
- 80. «Служба кровию и смертию». Дети боярские и рейтары
- 81. «Служба кровию и смертию». Однодворцы
- 82. Древние арии – кто они были и откуда?
- 83. Как стать миллионером
- 84. Когда рак на горе свистнет
- 85. Когда рак на горе свистнет. Альтернативное жульничество – 1
- 86. Когда рак на горе свистнет. Альтернативное жульничество – 2
- 87. Когда рак на горе свистнет. Альтернативная онкология, далее везде
- 88. Памяти сына
- Сноски из книги
- Содержание книги
- Популярные страницы
- Материалы и текстуры
- Вспомогательные материалы
- Множественные материалы
- Материалы для публикации
- Материалы
- Глава 4 Контролируемые организацией PR-материалы, предназначенные для внутренней аудитории
- Как упаковать свои материалы в готовый продукт
- Блок № 17. Бесплатные материалы
- Дополнительны ематериалы
- Дополнительные материалы. Образцы резюме
- Получите дополнительные материалы для читателей книги!
- Видеоматериалы